Our Approach
Mitsui Kinzoku Group, which has roots in the development of resources and the smelting business, is expanding the domains of the products and services from non-ferrous metals to various functional materials for the electronics and other industries, the manufacturing and assembly of functional parts for automobiles, the provision of technical services in the engineering business, and others.
We revised the Basic Quality Policy in 2022 as the standards for our resolute efforts to achieve quality in each business area and site in Japan and overseas. Each employee will understand and practice the policy so that our products and services will satisfy all our customers.
Fundamental Quality Policy
At the Mitsui Kinzoku Group, each employee will understand and practice the Fundamental Quality Policy so that our products and services will satisfy all our customers.
- We consider opinions from markets and customers as an asset, which enables us to anticipate future needs and promote efforts for optimal quality and customer satisfaction.
- We endeavor to invent, develop and provide innovative products and services by leveraging our Material Intelligence, while aiming to contribute to society.
- Viewing the quality of work as essential to good product quality, we pursue quality improvements through enhancing teamwork and speed at work.
- We will ensure compliance with rules and standards related to our products and services.
- We will give first priority to ensuring safety and security for all our business processes, including those related to supply chains, and disclose accurate information, as appropriate, related to quality and safety.
Revised in April 2022
* Fundamental Quality Policy applies to all sites of the Mitsui Kinzoku Group worldwide.
Reinforcement of the Quality Assurance System
Mitsui Kinzoku Group established the Quality Assurance Department in order to strengthen the group-wide quality assurance system. In addition, quality assurance department in each business line has become independent in order to strengthen quality assurance functions. The Quality Assurance Department at the head office, the Technical Department, and Quality Assurance Department of each business division make up the Quality Assurance Committee, which promotes planning and implementation of strengthening the quality assurance system of the entire group.
Quality Assurance System
Quality Compliance System
The Group promotes its quality compliance system in accordance with the Mitsui Kinzoku Group Quality Assurance Guidelines (QAGL). It includes reinforcing management system, improving reliability of experiment and inspection data, improving technology and securing quality assured, self-inspection by each business domain, and internal quality audit.
In FY2023, all sites in Japan conducted self-inspection on conformity to the guidelines. We also conducted quality compliance audits by internal third parties just as we did in FY2021 and inspected the status of development of quality compliance systems in 17 sites in Japan and overseas as scheduled. Additionally, in 2024, we are working on strengthening the quality compliance system by revising the "Quality Compliance Incident Judgment Criteria" used for self-inspections and quality audits in accordance with the QAGL at each site.The revision focused on the judgment criteria and the communication flow when quality compliance violations are discovered.
Photo: (Left) Internal quality audit at an overseas site Photo:(Right) Internal quality audit at a site in Japan
Quality Management System Certification
Each business unit conducts appropriate quality control following the quality management system. The manufacturing sites which need to get certification for quality management are officially certified for their quality management such as by ISO9001 and IATF16949.
We have acquired ISO9001 certification at 39 manufacturing sites in Japan and overseas. We have acquired IATF16949(formerly ISO/TS16949) certification, which is a specification for the automotive industry, at 17 manufacturing sites in Japan and overseas (as of the end of March 2024).
Number of claims at sites that hold QA meetings
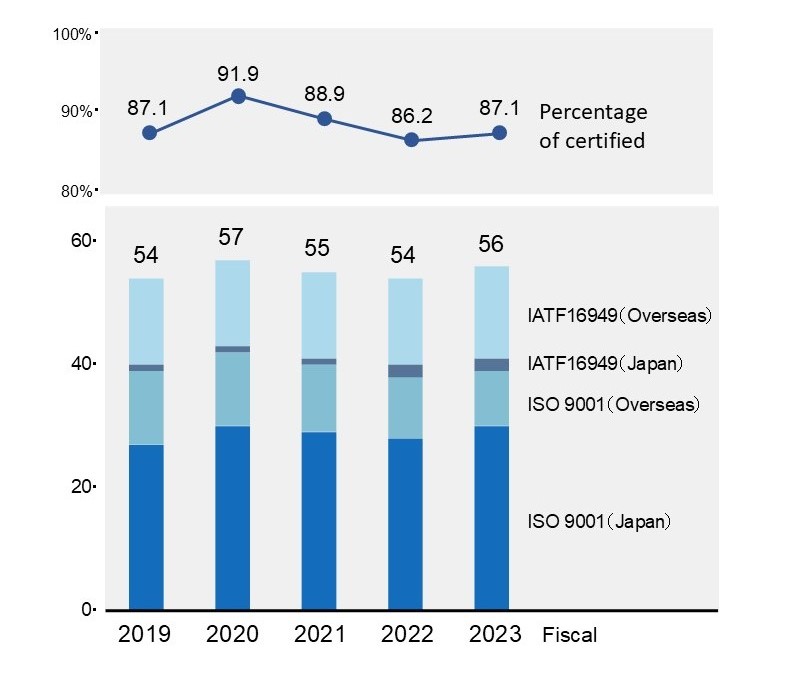
Quality Assurance Month Initiatives in 2023
During the "quality month" (November), the followings initiatives were implemented for all employees in our group to raise awareness for quality.
- Sending a message from the CEO on quality assurance and soliciting slogans and PC wallpapers from employees
- General training on quality compliance: conducted at all affiliates (Performance in FY2023:33 in Japan and 22 overseas)
- Conducting a knowledge and awareness survey on quality compliance every two years
- Conducting unique quality month events and their recognition at each site
Quality Control Training and Group Activities (GK)
We conduct quality control training in groups or online for employees to acquire management skills that help improve quality. We provide trainings for employees at all levels, from basic training for new employees to specialized training in statistics, Industrial Engineering and process thinking.
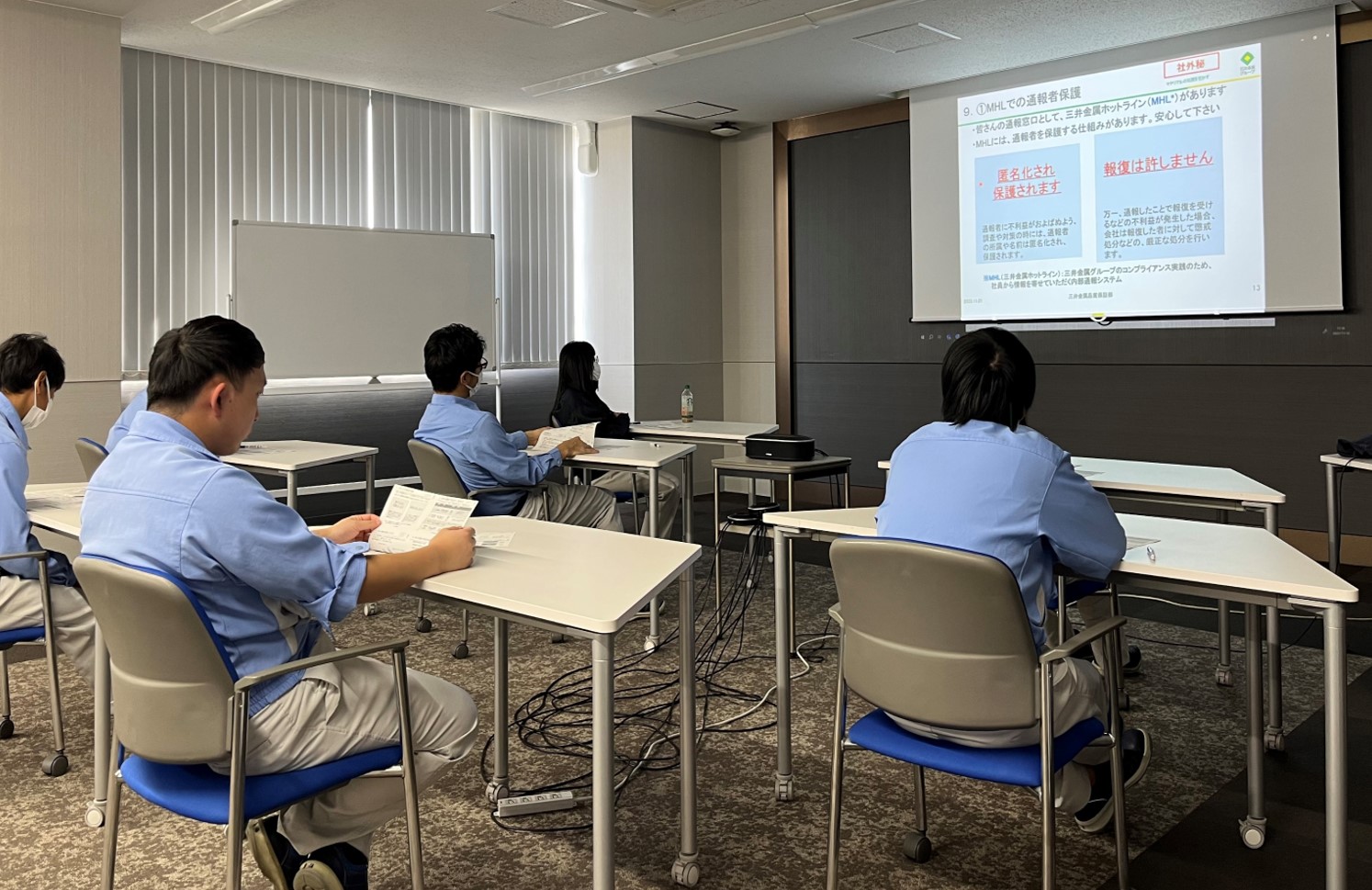
Photo: Training at a site in Japan
All employees are engaged in small group activities (GK) with the aim of developing human resources, revitalizing the workplace, and improving work. In the GK, we are striving to improve the quality of work to contribute to constitutional improvement.
At the same time we aim at “human development” to respect the human nature of each employee, draw out their abilities and make workplace truly creative and vibrant. In recent years, the GK activities have become widespread not only in Japanese sites but also in overseas ones.
Photo:(Left) The GK presentation for FY2020 was conducted online(commemorative photo of the attendees)
Photo:(Right) Confirmation of the actual items at the GK meeting in China
Results of Quality Management
Product-related accidents and recalls
In FY2023, non-compliance incidents didn’t happen regarding four Japanese product safety acts and product liability in the Group. Additionally, there was no product accident and product recall.
Products safety information provision
Mitsui Kinzoku Group shares products safety information with customers through specification form, technical documentation and SDS (Safety Data Sheet). In FY2023, non-compliance incidents didn’t happen regarding information provision and display of products and services. Additionally, to promote the provision of appropriate information about our products and services to customers and society, we are advancing the formulation of the “Product Information Provision Guidelines.“
Quality Complaints from Customers
The graph on the right shows the number of quality complaints in 13 business domains in Japan. In FY2020, it increased due to changes in aggregation standards and expansion into new markets entry into new fields in some projects, however, in FY2023, it decreased from FY2022 as a result of each of the initiatives.
Number of claims at sites that hold QA meetings
* The values expressed as relative values, with the data of FY2013 being 100